A new discovery by University of Lethbridge researchers that sheds light on a complex chemical structure found in bitumen may enable companies working in Canada’s oilsands to operate more efficiently and reduce their environmental footprint.
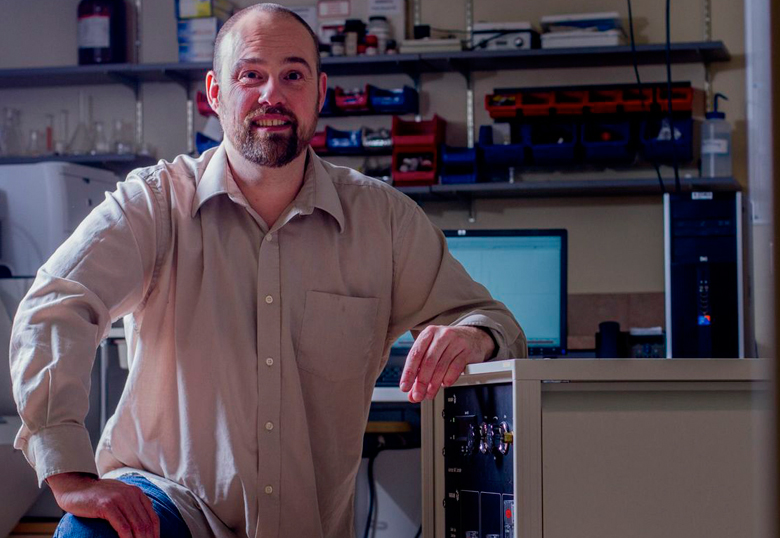
Three members of the Department of Chemistry and Biochemistry at the U of L, in collaboration with a private sector oilsands researcher, have established the architecture of asphaltene, the heaviest element in bitumen. Asphaltene has been found to interfere with the processes for extracting and upgrading crude oil.
The finding makes it possible to develop more effective and cleaner techniques for pumping and refining synthetic crude. The research, which took place at the University’s specialized Magnetic Resonance Facility, was published in the November/December 2013 edition of Energy & Fuels, one of the most cited journals in oil chemistry research.
“Asphaltenes throw a wrench into oilsands production, because they cause the oil to become very thick and viscous, and hard to treat chemically. By knowing their structure, it becomes possible to develop processes to break them down or modify them,” says Dr. Paul Hazendonk, a researcher with the U of L’s Canadian Centre for Research in Advanced Fluorine Technology (C-CRAFT).
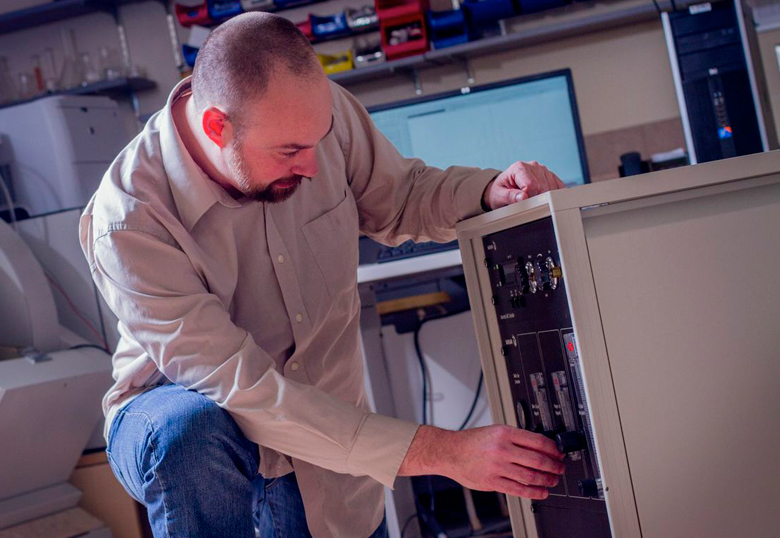
Asphaltenes are highly complex molecular structures made up primarily of carbon, hydrogen, nitrogen, oxygen and sulfur, as well as heavy metals such as nickel, iron and vanadium. In crude oil, asphaltene often forms into clusters that can block well bores, plug pipelines and deactivate catalysts that are used to refine it. As well, the presence of asphaltenes in petroleum significantly degrades fuel performance.
After two years of intensive research using nuclear magnetic resonance spectroscopy, the scientists were able to gain an in-depth understanding of the physical and chemical nature of asphaltenes, including the inter-molecular interactions that precipitate these troublesome clusters.
The finding has significant implications for oilsands companies looking to boost their productivity and stay competitive in this increasingly important segment of the Canadian economy. According to industry statistics compiled by the Alberta government, the region contains the third-largest crude oil reserve in the world.
In addition to potential productivity benefits, this research could help the industry lessen its impact on the environment. Currently, producing 100 barrels of synthetic crude requires a minimum of 20 barrels worth of oil equivalent in energy (from extraction, processing, upgrading, transportation and waste remediation), which equals 3.3 tons of oil that causes 10 tons of carbon dioxide emissions. By contrast, conventional oil has a ratio of 100 to 3.3 barrels, which equals 550 kg of oil that leads to 1.5 tons of CO2. If oil companies can develop better production processes, they will be able to operate more sustainably.
“If we can improve processes to make that ratio much better, that reduces the greenhouse gas emissions of the industry,” says Hazendonk, who is currently conducting new research with his team members to further explore asphaltenes. “So operations become leaner, more cost effective and more efficient from an energy usage point of view.”
The Canadian Centre of Research in Advanced Fluorine Technologies is the first Canadian centre focusing on research and training around the element fluorine. C-CRAFT brings together local, national and international teams with wide ranges of expertise in fluorine chemistry.